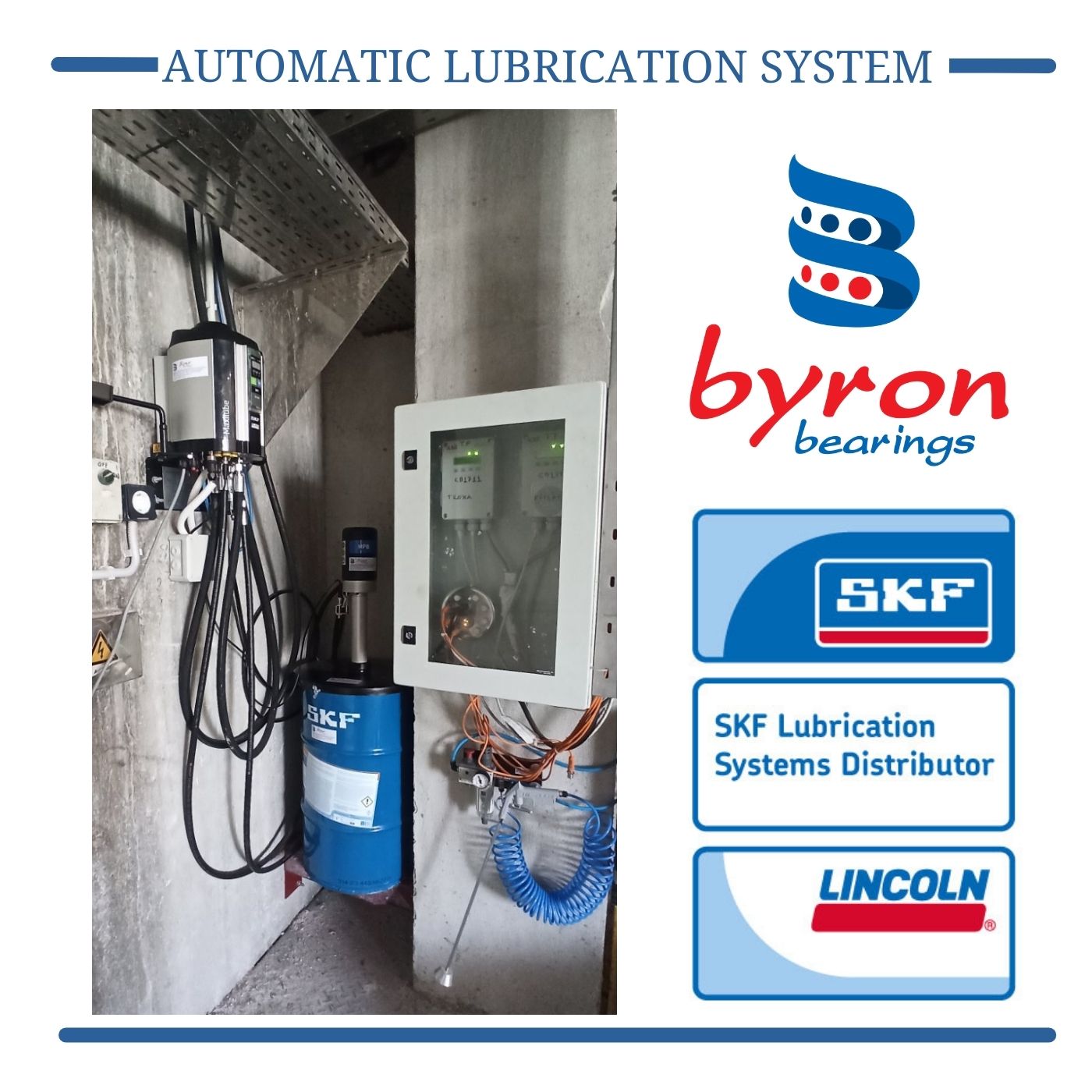
THE CASE
Production machines in the paper industry are sophisticated and diverse, tailored to meet the specific requirements of various paper types and qualities. Given the high production rates and continuous operation of these machines, effective maintenance strategies and lubrication systems are essential to prevent wear, failures, and accidents.
At a prominent and key paper manufacturer in northern Greece, our team implemented an advanced solution to modernize the papermaking machine, redefining industry standards.
THE CHALLENGE
The papermaking machine operates in an extremely demanding environment with frequent washdowns using water and chemical cleaners, as well as limited space. Running 24 hours a day, the machine allows for minimal downtime for maintenance. Manual lubrication of the roller bearings not only posed safety risks but also required significant manpower, particularly for tasks in hard-to-reach, inconvenient, and hazardous locations. Furthermore, the existing manual lubrication process lacked precision in determining the required lubrication amounts for maximizing bearing lifespan.
THE SOLUTION
To address these challenges, Byron Bearings SA seamlessly proposed and implemented a solution for this leading paper manufacturer.
SKF Centralized Automatic Lubrication System
Utilizing the SKF Maxilube system, an automated lubrication solution, precise amounts of grease are delivered to the necessary machine points at the right time. This automated process minimizes manual intervention and ensures consistent, optimal lubrication levels. Our implementation focused on the automatic lubrication of 32 bearings in the canvas roll and felt roll cylinders.
SERVICES PROVIDED
• Design and technical calculations for system layout, pipe sizing, and lubrication amounts and frequencies
• Schematic drawings with mechanical and electrical details
• Installation services for main components and piping
• Mechanical and quality supervision during installation
• System commissioning upon lubrication system startup
• Product training for the customer
THE RESULT
Our solutions led to improved machine performance and maintenance efficiency, with the following proven results:
- Bearing failures in roller shaft bearings and machine breakdowns have significantly decreased, ensuring smoother operation.
- Bearings now reach their maximum lifespan, contributing to the overall reliability of the equipment and production process.
- Maintenance operations have become faster and more efficient, greatly enhancing safety conditions for the maintenance team, especially in hazardous and hard-to-access lubrication points. The elimination of manual lubrication has streamlined operations.
- The installation was successfully completed with zero accidents within 385 labor hours, highlighting our commitment to safety and reliability.